Guest blog: How shipbuilding can chart a course for maritime 4.0
There is no doubt that Industry 4.0 has driven dramatic changes in the manufacturing of products, machinery, and equipment. Its impact can clearly be seen in many aspects of discrete A&D manufacturing—the creation and assembly of items by components used to manufacture highly complex military platforms such as aircraft is just one example. But the full impact of Industry 4.0 is yet to be felt in military and commercial shipbuilding—where building processes are of a size and scale more similar to a construction project than even the most complex product manufacturing.
Shipbuilding in the digital era
Australian Industrial Transformation Institute explained the rationale and motivation for the adoption of Maritime 4.0: “In line with all other forms of manufacturing, Industry 4.0 offers a vision for transformation of the shipbuilding industry through the establishment of ‘Digital Shipyards’ and the adoption of a ‘Shipyard 4.0’ agenda.”
Maritime industry forecasts correlate with this increased digital focus. ResearchAndMarkets data suggests that the digital shipbuilding sector is set to grow quickly over the next few years—from $591 million in 2019 to $2.7 billion by 2027, with an impressive 21.1% compound annual growth rate.
According to a recent study in the Procedia Manufacturing industry journal published as part of the International Conference on Industry 4.0 and Smart Manufacturing, Maritime 4.0 allows:
- The automated integration of real data into decision-making
- The adoption and implementation of connected technologies for design, production, and operation
- Reduction of vessel environmental impact related to production, operation, and disposal (including emissions, underwater noise, and material utilization)
- Affordable and sustainable operations
- Reduction of risk, increasing safety and security
There is a clear industry move towards Maritime 4.0, but it brings challenges, not only in terms of complexity of processes but also in supporting IT infrastructure. With this in mind, there are four key areas to address in any military or commercial Maritime 4.0 strategy.
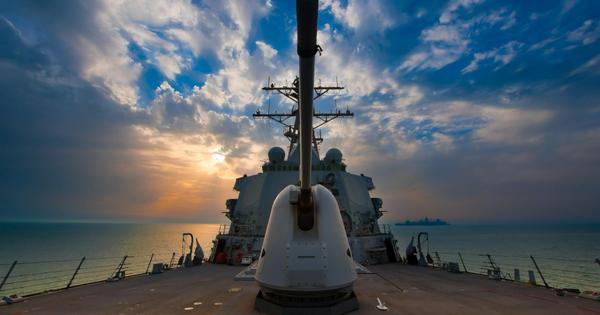
1. Complex projects breed complexities that need full proper support
Difference in scale means difference in kind—manufacturing a sea vessel is more akin to managing a full-scale construction project than traditional manufacturing of parts and products. Manufacturing a complex, state-of-the-art asset requires supporting systems to effectively manage a full-scale construction project. Even commercial shipbuilding, though often less complex in design, comes with its own set of complexities—stringent import/export rules that vary widely by country, new requirements for infectious disease control, and high labor costs, just to name a few.
Global competition is fierce and dominated by low-cost labor countries: More than 90% of global shipbuilding takes place in just three countries—China, South Korea, and Japan. Coming to grips with such complexity requires the support of an industry-specific and enterprise-breadth system that can manage such a unique manufacturing process. Thus, supporting project management and supply chain processes is critical.
2. Technology plays a major role in shipyard transformation
The transformational technologies essential to Industry 4.0, from AI and machine learning to 3D printing and digital twins, will play a defining role in Maritime 4.0 strategies. Taking advantage of these technologies requires digital transformation, and because of the complexity of the projects, requires a digital shift to a more integrated environment.
A fully digital shipyard needs to be underpinned by a software system that’s agile enough to act on the increasing data volume and complexity to deliver quantifiable operational benefits. That means any successful naval or maritime digital transformation program will involve putting in place a full Integrated Data Environment (IDE) requiring close collaboration from military organizations, industry players, and software providers.
IFS customer, submarine, and warship builder ASC, Australia’s largest defense prime contractor, recently announced a company-wide digital transformation program. The comprehensive program will set the ground for the ASC transition to become a digital shipyard—facilitating more streamlined processes, enhanced integration between systems, and the expanded use of real-time data to drive optimized decision-making across the organization.
3. High levels of security across the maritime ecosystem to support the digital thread of critical data
The IDE and digital backbone supporting Maritime 4.0 will not come without its challenges—and cybersecurity will be just as pervasive in the shipbuilding sector as in any other, as recognized by a recently published U.S. Congressional Research office paper on U.S. Navy force structure and shipbuilding plans:
“The digital thread from manned ships and autonomous platforms provides enormous opportunities for efficiencies in coordination, operation, maintenance, and cyber-resilience. However, this thread of critical data, including location, heading, and platform health, presents one of the biggest opportunities for cyber threats and cyber-attacks to Navy vessels. End-to-end cybersecurity and anti-tamper technology need to be addressed for many systems, from small man-portable autonomous vessels to systems as large as carrier groups.”
The defense sector has been well ahead of the curve when it comes to cybersecurity best practices—and shipbuilders servicing military customers will need to ensure compliance with strict regulations. Regulatory-compliant software can be a key differentiator when bidding for ship manufacturing contracts. Enterprise software should be a strategic enabler for information assurance and cybersecurity to address risk and threats throughout all phases of the software development life cycle.
4. Sustainability at the core of maritime strategy
Maritime sustainability has been a huge focus area in recent years—and Maritime 4.0 will, of course, positively impact sustainability efforts. The International Maritime Organization IMO has been spearheading an industry-wide effort to accelerate a major fuel and technology transition in response to the climate challenge—its goal is to reduce annual CO2 emissions by at least 50% by 2050. At the same time, military forces are also looking at greener operations for newly built ships. The UK Royal Navy recently implemented a catalytic reduction system in two of its newest warships that reduce nitrogen oxide emissions by up to 97%.
Good supply chain optimization can help manage composite materials, and new manufacturing techniques will drastically reduce unnecessary emissions. Again, IDE has a key role to play here. When shipbuilding data is funneled through one system, enterprise software can assign a sustainability score to every process across a shipbuilding organization’s value chain.
Helping shipbuilders plot a course across the digital chasm
Driven by key Industry 4.0 technologies and widescale digital transformation within naval forces, the military and commercial shipbuilding sectors are poised for “Maritime 4.0”. But making this digital shift involves grappling with complex projects, components, and data on a scale way beyond traditional Industry 4.0 manufacturing. Because of the size of their operations, ship manufacturers and naval organizations need to move towards an IDE to capitalize on the efficiency, visibility, security, and sustainability benefits of Maritime 4.0 in an increasingly digitized sector.
Read more about Maritime 4.0 and the rise of the digital shipyard in this white paper.
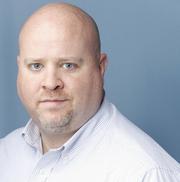
Matthew Medley ensures IFS solutions meet the demanding needs of Defense Operators, In-Service Support Organizations, and Manufacturers worldwide. He has served as a management consultant, program manager, and project manager in aerospace, defense, and manufacturing organizations including Porsche, Lockheed Martin and others. A graduate of the US Air Force Academy, Matt served as a Major in the US Air Force, compiling over 2,500 flight hours in the C-130 aircraft. He holds the FAA Airline Transport Pilot and Certified Flight Instructor ratings and has earned multiple postgraduate degrees and certifications including an MBA from Kennesaw State University and PMI’s Project Management Professional certification.